Precision Machining
5 Axis Milling
As medical devices become more complex, so too, do their constituent components and with that, the injection moulds that produce them. 5 axis milling broadens the possibilities available to Priors to manufacture components with the most intricate geometry.
Where once a simple component required up to six set up operations for completion on a 3 axis milling machine, a 5 axis milling machine may need as little as one or two at most. More complex components that previously would have been impossible to form on a 3 axis milling machine are now easily shaped. Through the elimination of unnecessary setups, the accumulation of positioning errors introduced during setups are no more, leaving parts seamless on all surfaces. Complex 3-dimensional contoured surfaces can be high speed machined with sub-micron accuracy and tool control so smooth that it leaves a near polished finish, thereby minimising or even eliminating the need for additional manual operations.
Priors incorporates a range of 5 axis milling machines into its mould building and metrology fixture workflow, from world class German and Japanese machining centre manufacturers. DMG Mori DMU 50, Mori Seiki NMV1500 DCG and Kern Micro HD are to name a few. Depending on the job at hand, Priors can optimise speed and precision to deliver components that meet demanding specifications in rapid lead times.
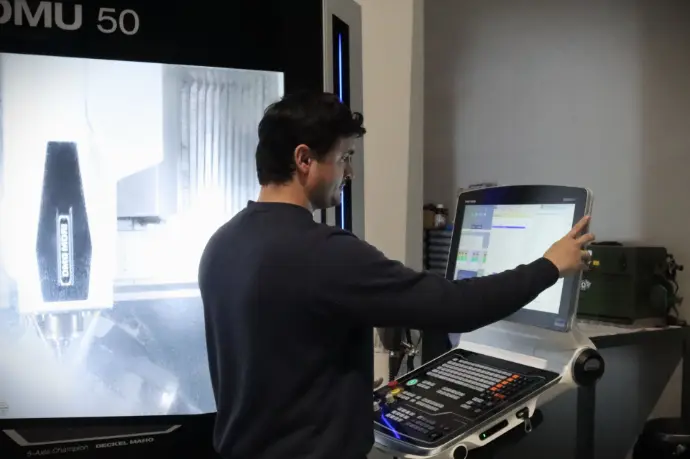
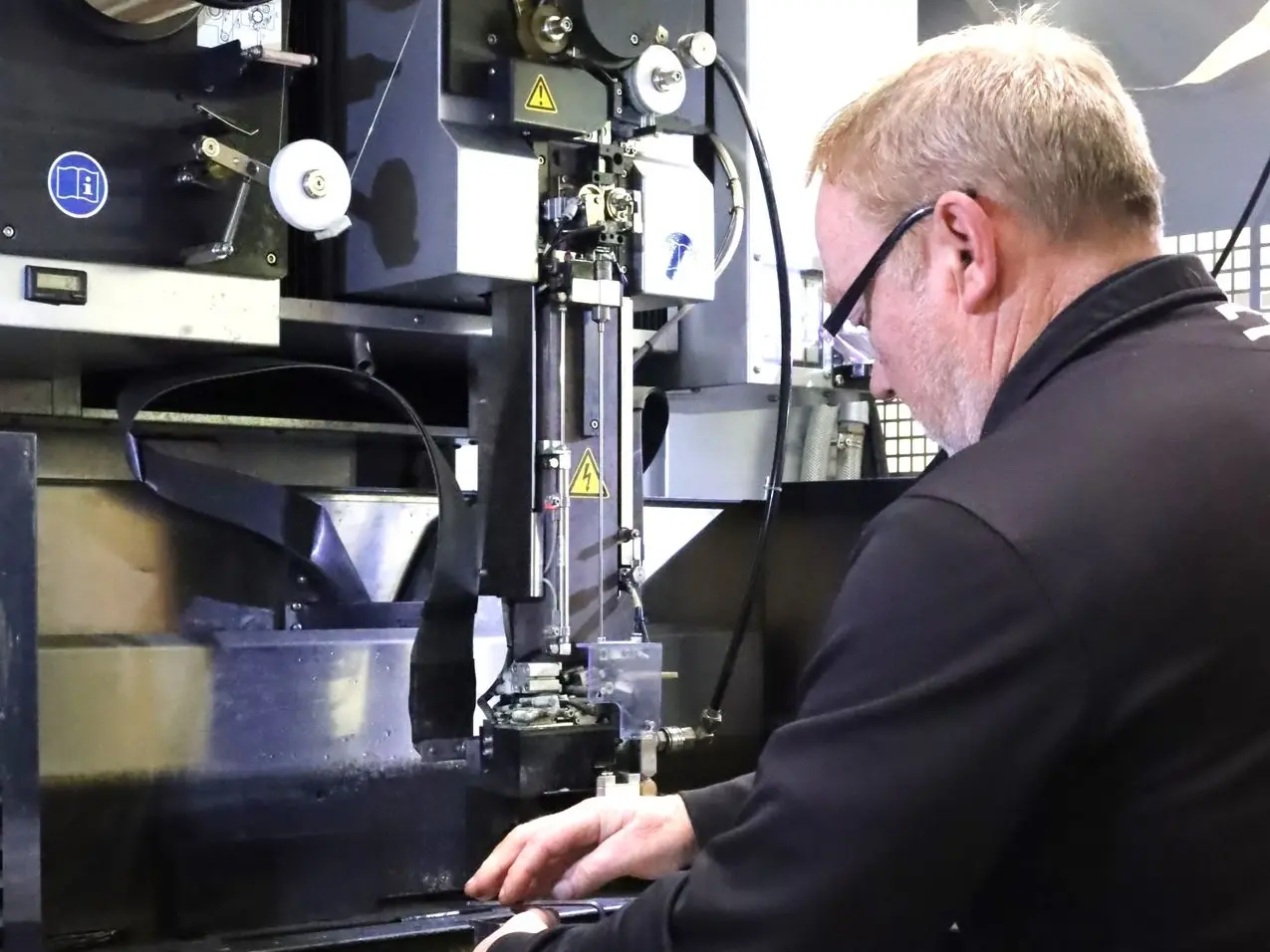
Wire Erosion
Wire Erosion is a cost effective method that enables a hardened workpiece to be cut through with a high accuracy. The process relies on an electrical discharge from a wire electrode, which erodes the workpiece into the form required. With absolute control of the electrical discharge and position of the wire relative to the workpiece, intricate details can be eroded into the workpiece without a burr. As the process relies on the electrical discharge to cut the material, any conductive material can be cut, irrespective of its hardness.
While other machining processes may struggle to fixture small components, the nature of the wire erosion process, which does not rely on high force during the cutting process, enable small components to be cut without damage from fixturing. Control of the electrical discharge and related parameters, can produce a range of surface finishes.
Electrical Discharge Machining (EDM)
Electrical Discharge Machining (EDM), commonly referred to as spark erosion, is the corner stone of high precision mould making. EDM can achieve geometries and tolerances that are not possible with other traditional machining methods such as milling. With over 40 years experience in EDM, Prior PLM Medical has established a dedicated team to enable in-house mould manufacture and repair.
The EDM Process has 3 main steps, Electrode Design, Electrode Manufacture and EDM.
The Electrode set is manufactured to form a specific cavity geometry. The manual or CNC EDM machine can then begin the EDM process. This involves repeated and progressive erosion of the workpiece, with electrical discharges removing material to the desired dimensions.
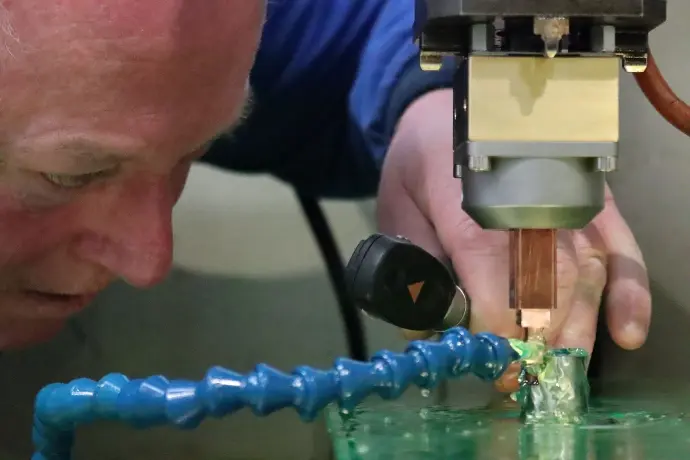
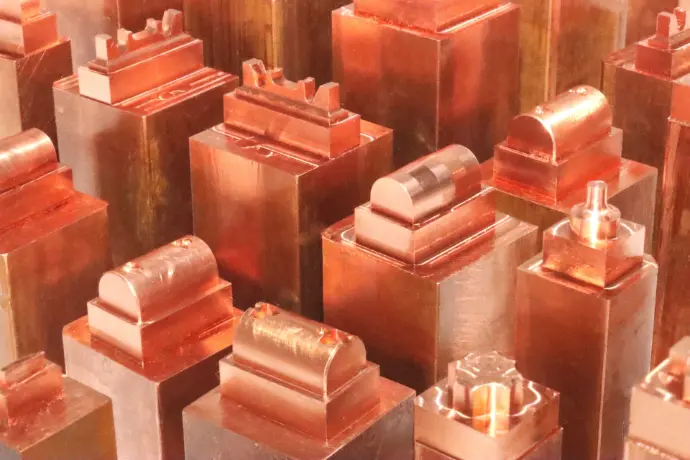
EDM Electrode Design and Manufacture
With the final cavity geometry in mind, a set of electrodes are designed to obtain the cavity dimensions. The quantity of electrodes required for a typical cavity range from 4 to 40 electrodes. With dedicated and experienced Electrode designers in-house, Prior PLM Medical is able to rapidly generate the electrode designs required for the project.
Prior PLM Medical has invested in 3 high speed milling machines for manufacturing Electrodes on demand. The ability to machine Graphite or Copper electrodes, is a critical in-house capability.
Grinding and Fitting
Grinding and Fitting are an essential process enabling micron accuracy on interfacing surfaces. Parts are ground post heat treating to ensure the desired surface flatness or cylindricity are achieved. The experienced Priors Grinding and Fitting team have over four decades of fitting experience between them and are able to achieve tight tolerances on the most challenging of parts and materials.
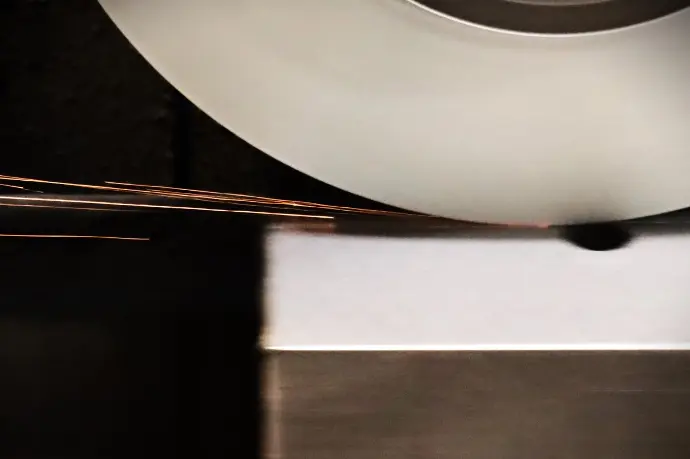
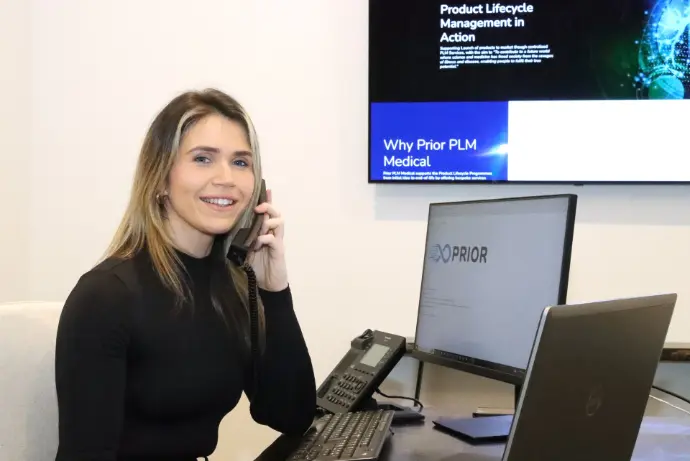