Injection Mould Solutions
Overview
Prior PLM Medical have 40 years of experience designing and manufacturing complex injection moulds. Our “user first” approach to mould development involves working with our clients to identify the critical aspects of their design, allowing us to avoid excessive tool complexity, thus reducing lead times and cost for our clients without sacrificing reliability, functionality or the aesthetics of the component.
With the 'first principles' approach to manufacturing through our PLM model we understand the subtleties between design specification and product realisation. Our expertise derived from 40 years of successful projects, provides our clients with unique insights into the relationship between tool and product design and how that translates into manufacturability.
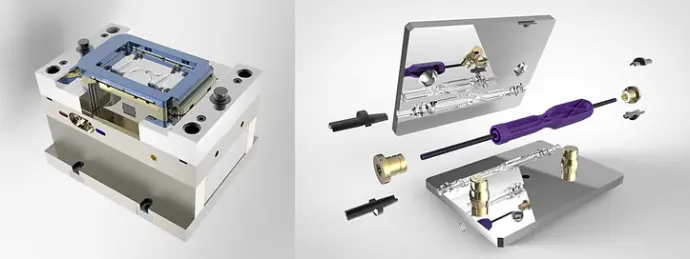

Capabilities
We offer a range of mould solutions to suit projects from the R&D stage to pre-production, validation and all the way to full production. Some of our more notable services are:
• MoldFlow Analysis
• Cassette Moulds
• Insert moulds
• Micro moulds
• Multi-shot moulds
• Unscrewing
• End of Arm Tooling (EOAT)
• Palletisation Systems
• De-moulding Fixtures
Mould Flow Analysis
Before we commit a tool design to steel, we use industry leading simulation software, which can predict cavity flow characteristics allowing us to identify potential issues such as trapped air, short shot, weld lines and sink marks among others.
Our expert mould design engineers carefully assess simulation assumptions, prepare mesh geometry and verify it using techniques such as mesh convergence studies to ensure the results are accurate. We then display these results, such as temperature, pressure or defect types in intuitive plots and graphs that enable our customers and their stakeholders to visualise how the mould is filled and informs our design team on what improvement can be made.
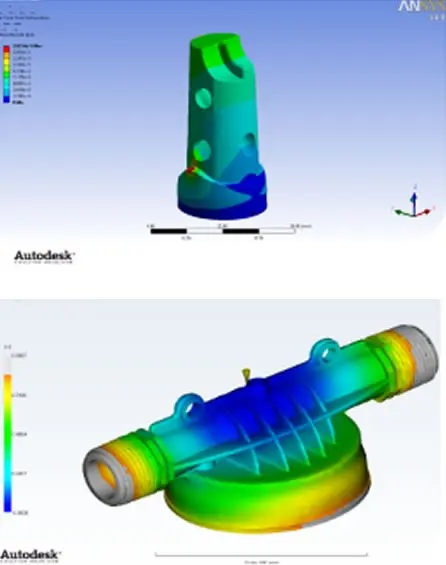
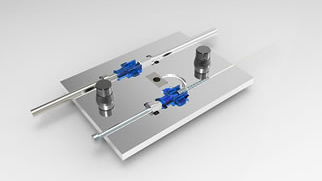
Cassette Moulds
Cassette moulds are prototype moulds that fit into standard mould bases. This eliminates the need to design and manufacture expensive and time-consuming mould bases as would be required with a production tool. Prior PLM Medical has a range of mould bases that suit cassettes across a wide range of sizes and forms.
The key benefit of a cassette mould is the limited risk during mould development. Cassettes are used to dial in critical dimensions, gate location and type, venting requirements, and moulding parameters such as temperature, pressure, and time. This data gives customers confidence that their product functions as intended and that, when their product graduates to a production mould, quality and dimensions are pre-established. The components in a cassette mould are semi-automatically or manually de-moulded making it suited to small production runs of up to 150 shots per shift.
Production Moulds
Prior PLM Medical offers a variety of production mould design and manufacturing services. We understand that automation is critical in the modern manufacturing environment and as such, we assist our customers in implementing the production mould into a fully automated cell, incorporating moulding, de-moulding, inspection, assembly, finishing and any other ancillary processes. We have experience with a range of traditional and advanced moulding technologies including conformal cooling, diffusion welding, pressure transducers, temperature transducers and safety sensors.
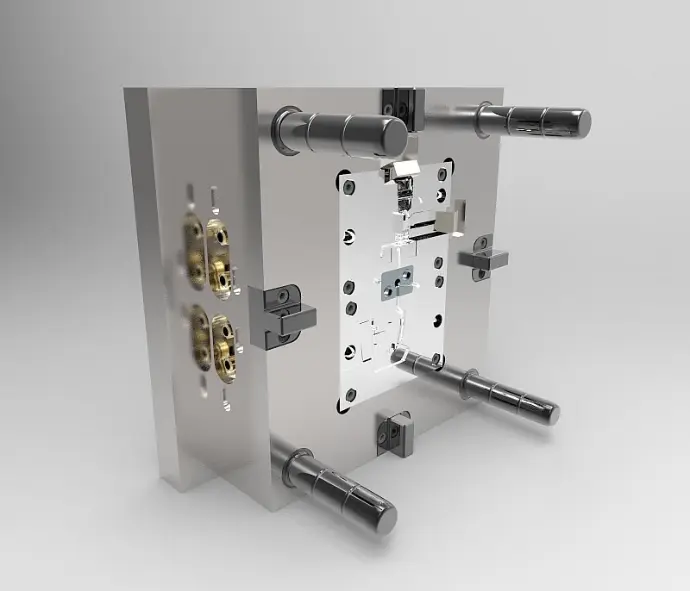
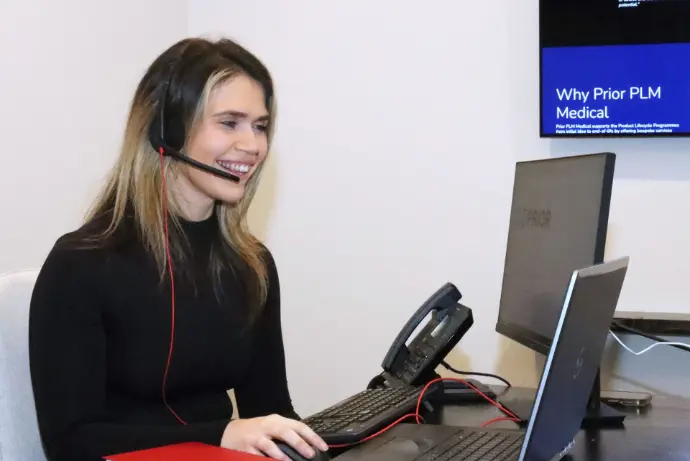