Pilot Manufacture
Overview
The Pilot Manufacturing Division specialise in the Injection Moulding of medical and pharmaceutical components. With a focus on the prototyping, clinical and pre-launch moulding, we assist our customers in the rapid development of injection moulded components.
With extensive experience in a wide range of polymers, from Polypropylene to Thermoplastic Polyurethane, we can mould and overmould the most challenging of components.
Following recent advancements in the sustainability and innovation of polymers we can, not only test these new materials, but also optimise and validate the process, allowing us to manufacture components for use in medical devices and clinical trials.
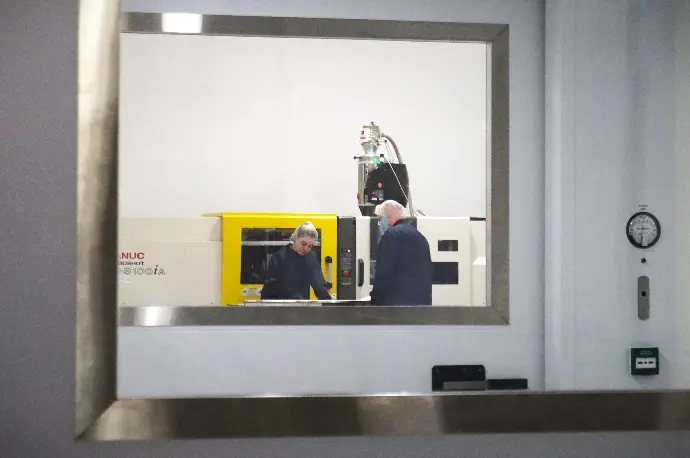
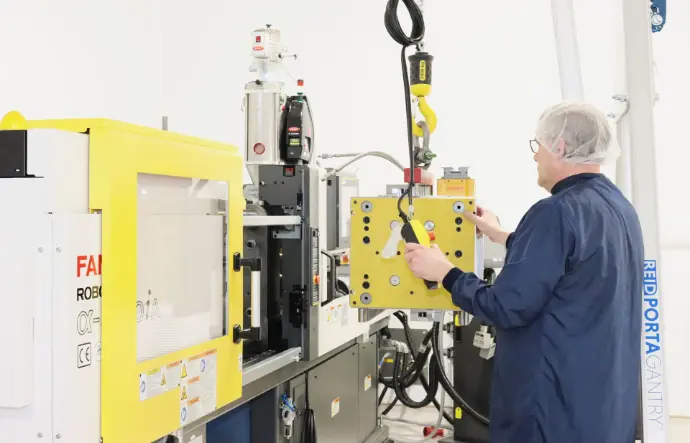
Services
• ISO Class 8 Cleanroom Moulding
• Cleanroom Assembly
• Non-Cleanroom Moulding and Assembly
• Tool Trials
• Injection Moulding Process Development
• Process Validation
• Production Component Manufacture
Facilities
• Injection Moulding Capabilities from 50t to 150t
• Range of Barrel and Screws
• Material Dryers
• Hot runner controllers
• Mould handling and storage
• Material warehousing
Process Development
Prior PLM Medical offer a comprehensive Injection Moulding Process Development service, which assists our customers establish a repeatable molding process.
Using the Scientific Moulding approach as implemented through the Helix Polymer Software, we are able to refine the process and identify potential process strengths and weaknesses.
Once initial parameters are established it is important to identify an optimised nominal process. A standard study enables the selection of such nominal parameters through the execution of various studies as shown below:
• Mold Configuration
• Barrel and Material Temperatures
• Rheology Curve
• Melt Preparation
• Cavity Balance
• Filling Profile
• Packing Time and Pressure
• Mould Movement
• Cooling Time
• Clamp Force
• Weight Variation Study
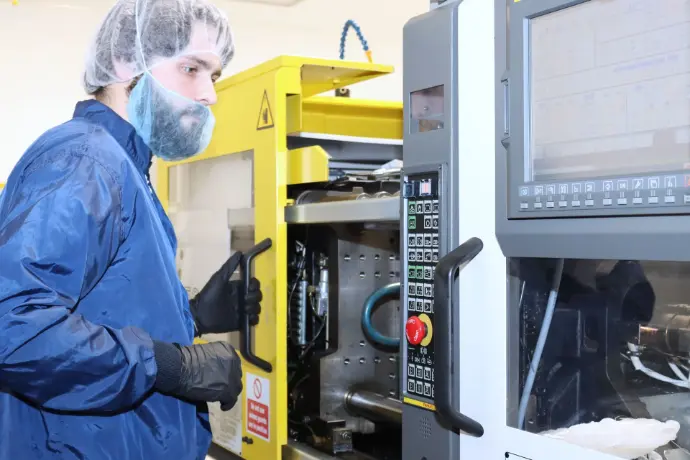
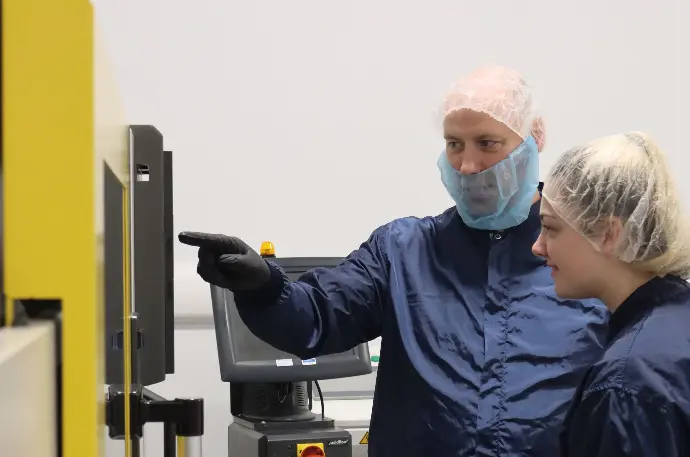
Production
Prior PLM Medical have developed our Moulding capabilities to allow us to undertake Injection Moulding contracts ranging from low volume Clinical Builds through to large scale batch production. With a focus on rapid turnaround times and the PLM model, we enable our customers to progress through the product development life cycle in as short amount of time as possible. All our Injection Moulding is carried out within the regulatory requirements of the ISO 13485 Quality Management System.
To comply with best practice Medical Device Injection Moulding, we have recently invested in our 160m² ISO Class 8 cleanroom.
Our production staff are trained to carry out in process Inspection of components. Full dimensional inspection of components can be carried out in our Metrology Services department. Our cleanroom is closely supported by our MRO division who are on hand to rapidly address tooling issues.
We provide our customers with a comprehensive range of services from Medical Device component manufacture, through to the assembly of devices or device sub-assemblies. To enable this, we have included an assembly area within the cleanroom which allows us to undertake assembly of injection moulded components, thus ensuring parts are manufactured and assembled without leaving the cleanroom.
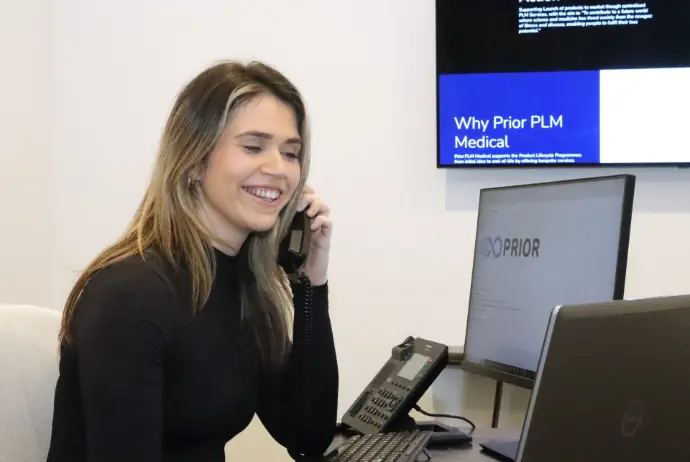